The Environmental Impact of Solid Surface Manufacturing and How We Mitigate It
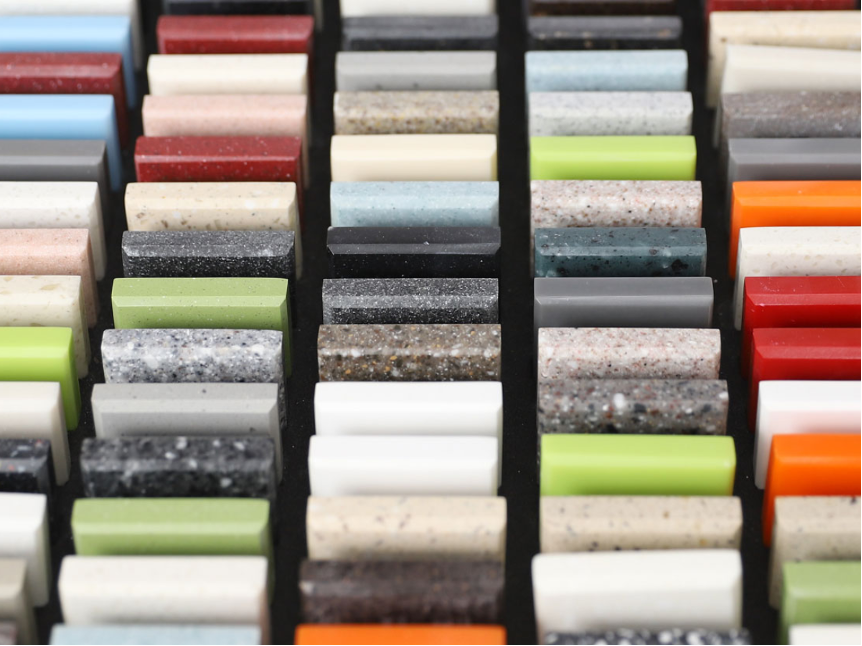
Introduction
Solid surface materials have become increasingly popular in both residential and commercial applications due to their durability, versatility, and aesthetic appeal. These materials, often used for countertops, sinks, and other surfaces, offer seamless integration and a wide range of design options. However, as the demand for solid surface products grows, it is crucial to understand the environmental impact associated with their manufacturing. Assessing the ecological footprint of solid surface production helps in identifying areas for improvement and encourages the adoption of sustainable practices, ultimately contributing to a healthier planet. KKR Stone, the leading solid surface manufacturer, is at the forefront of these sustainability efforts.
Understanding Solid Surface Manufacturing
Solid surface materials are primarily composed of acrylic, polyester, or a blend of both, often combined with natural minerals such as aluminum trihydrate. These components are selected for their ability to create a non-porous, durable, and visually appealing surface that can be molded into various shapes and sizes.
The manufacturing process typically begins with the mixing of the raw materials to form a resin. This resin is then poured into molds to create sheets or specific shapes. The curing process involves heating the resin to solidify and strengthen it. Once cured, the material is cooled, trimmed, and polished to achieve the desired finish. This process may also include the addition of pigments to create a wide range of colors and patterns.
While the production of solid surfaces is efficient and results in a high-quality product, it is important to consider the environmental implications of the materials and processes used.
Environmental Impact of Solid Surface Manufacturing
Material Extraction and Resource Use
The production of solid surface materials involves the use of non-renewable resources such as fossil fuels and bauxite. Acrylic and polyester resins, essential components, are derived from petroleum-based products, contributing to the depletion of fossil fuels. Additionally, the extraction of bauxite, used in aluminum trihydrate, impacts the environment through land degradation, deforestation, and biodiversity loss. These processes not only consume significant natural resources but also lead to environmental degradation.
Energy Consumption
Manufacturing solid surface materials is energy-intensive. The production process, including mixing, molding, and curing, requires substantial amounts of energy, primarily from non-renewable sources. Comparatively, the energy consumption for producing solid surfaces is often higher than that for natural stone materials like granite but can be lower than for engineered quartz, depending on the specific manufacturing practices. Advancements in technology and energy-efficient processes are crucial to reducing the overall energy footprint of solid surface manufacturing.
Waste Generation
The manufacturing process generates waste, including off-cuts, trimmings, and defective products. The composition of solid surfaces, often a blend of various resins and minerals, poses challenges for recycling. Unlike materials that can be easily separated and repurposed, solid surfaces require specialized recycling processes, which are not always widely available. As a result, a significant portion of production waste may end up in landfills, contributing to environmental pollution.
Understanding these environmental impacts is essential for developing more sustainable practices in the production of solid surface materials.
Mitigating the Environmental Impact
Sustainable Material Sourcing
To mitigate the environmental impact of solid surface manufacturing, many companies, including KKR Stone, are turning to recycled and eco-friendly raw materials. By incorporating recycled acrylic and polyester resins, manufacturers can reduce the reliance on virgin petroleum-based products. Additionally, sourcing natural minerals from sustainable and responsibly managed quarries helps minimize the ecological footprint. Efforts are also being made to explore alternative, renewable resources, such as bio-based resins, to further reduce dependence on non-renewable resources.
Energy-Efficient Manufacturing Processes
The implementation of energy-efficient technologies is crucial in reducing the energy consumption associated with solid surface production. Advances such as high-efficiency curing ovens, optimized mixing processes, and improved insulation in manufacturing facilities help lower energy use. Moreover, some manufacturers, including KKR Stone, are investing in renewable energy sources, like solar and wind power, to offset the energy required for production. These initiatives not only decrease the overall energy footprint but also contribute to a reduction in greenhouse gas emissions.
Waste Reduction and Recycling Initiatives
Minimizing waste generation is a key strategy in sustainable manufacturing. Companies are adopting lean manufacturing techniques to improve material efficiency and reduce off-cuts and trimmings. Innovations in production processes, such as precision cutting and molding, further help in minimizing waste. Additionally, the development of recycling programs for solid surface materials is gaining traction. By establishing take-back schemes and recycling facilities, manufacturers can reclaim and repurpose waste material, closing the loop in the product lifecycle. This approach not only reduces landfill waste but also conserves resources by reintroducing recycled materials into the production process.
Eco-Friendly Product Design
Designing solid surface products with longevity and durability in mind is another significant step towards sustainability. Products that are built to last reduce the need for frequent replacements, thereby decreasing resource consumption and waste generation over time. Furthermore, the non-porous and easy-to-clean nature of solid surfaces minimizes the need for harsh chemical cleaners, promoting a healthier indoor environment. By focusing on durability and ease of maintenance, manufacturers like KKR Stone can create products that not only meet consumer demands but also align with environmental sustainability goals.
Through these combined efforts, the solid surface industry can significantly mitigate its environmental impact, paving the way for a more sustainable future.
Conclusion
Sustainable manufacturing practices are essential in reducing the environmental impact of solid surface materials. Continued innovation and commitment to eco-friendly methods are crucial for minimizing resource use, energy consumption, and waste generation. By prioritizing sustainability, the industry, led by companies like KKR Stone, can contribute to a healthier planet for future generations.